240 磅的静态重量正准备用于靠背耐久性测试。
1958 年,在 Charles Eames 和 Ray Eames 的推动下,George Nelson 和 Herman Miller 的老板 D.J.De Pree 建设了一处空间,供设计师进行产品原型实验和测试。六十多年后的今天,测试实验室的面貌已与开创之初大相径庭。这里曾经是一个堆满机械设备(电缆、滑轮、配重罐,甚至气动元件)的老式维修车间,现在则变成了一个飞机库大小的精密实验室,配备技术先进的机器,可以对速度和冲击力进行精确测量。
实验室位于密歇根州霍兰市设计场制造区的中心,两侧是制造者空间和产品设计工作室。这里可以称得上是工匠的实验室,更确切地说,是一个巨大的、闪闪发光的、充满重型机械的工匠游乐场。地板上贴着安全胶带,红绿灯忽明忽暗,昭示着一种秘密的机器语言。
空气中弥漫着耐久性测试机的节奏。配重袋毫不客气地掉落在座椅的椅座上。扶手垫随着压力的增减而晃动。滚轮连续旋转数天,这一切都是以设计背后的科学为名。
技术人员对从工作椅到可调节高度的办公桌,再到面板和工作台系统等各种产品进行了约 2,500 次不同的测试。承重和耐久性测试对最坏的情况予以再现:扶手挤压器、靠背倾斜器、脚垫收拢器。增加所悬挂架子上的重量,直到架子倒塌。机器对家具上进行惨无人道的拉伸。磨损模拟利用机器人技术,在较短的时间内重现数月、数年甚至一生的使用情况。技术人员通常通过再现故障的方式进行逆向工程。如果询问他们中的许多人,他们会告诉您失败才是乐趣所在。实验室测试服务经理、工程师 Kyle Wright 表示:“荣耀归于座椅,但面板系统、工作台系统需要进行承重测试,而这些测试要耗费大量人力,一个系统的自重可达 4–5,000 磅。”
BIFMA(商业与机构家具制造商协会)的指导方针为产品性能设定了行业标准,但 Herman Miller 的产品经常超出要求。就拿背部耐久性测试(或称“靠背”测试)来说,要求在 75 到 100 磅的压力下进行 120,000 次斜躺。Herman Miller 可实现 1,000,000 次循环。为什么会这样?最重要的是保修。测试的许多产品都有 12 年的保修期:没错,是 12 年,而且是全年 365 天、每周 7 天、每天 24 小时。对于技术人员来说,保修期更长:这关系到他们的诚信。Wright 说:“我们是质量的守门人。
要了解测试实验室的质量和诚信的重要性,就必须先看看它的起源。1948 年,Nelson 为 Herman Miller 设计了首个家具系列,随附的目录在前言中为包括质量在内的几项原则奠定了基础(这是十年后测试实验室的良好前兆)。
Nelson 写道:“您制造的产品非常重要。Herman Miller 和其他公司一样,受美国经济规则的制约,但我还从未见过为了迎合大众的价格档次,或出于其他原因而降低结构或表面处理质量的情况”。
1978 年,设计评论家 Ralph Caplan 在 Herman Miller 总裁俱乐部会议上发表了题为“Eames 与质量”的演讲。(他的演讲后来被写成了一篇文章《Doing Quality》。)他建议,要想做出“尽可能好”的设计,任何创造性的行为都必须包括“愿意失败”,这一想法转述自 Eames Office 的一名设计师 Peter Pearce。
“摇摆冲击”推车上有一个配重破坏球。
对这些产品进行弯折、旋转、戳刺、晃动、摔打和浇水等各种测试,有助于实现公司的可靠保修,甚至更多。有些椅子可能每天都会有不同的人坐上一整天,而另一些椅子则可能会世代相传。测试实验室高级技师 Curt Vanduren 说:“我们努力制造出经得起考验的产品。我们听说,‘这把椅子为什么这么贵?’我告诉他们,你们根本不知道这把椅子是怎么做出来的。不知道这把椅子能使用多久。”
Wright 说,一款产品可能需要三到五年的时间才能推出,分别有六到十种不同的结构,每种结构都要经过试验。有些测试是直接进行的,而有些则明显不是。他回忆起多年前一次特别难忘的系统测试,其中包括办公室面板和隔板。技术人员 Steve Arendsen 说:“我们用液压装置连接了所有设备,以模拟货架和工作台被拉倒的情况。拉倒后,几乎爆炸开来。我是说,面板都飞起来了。”
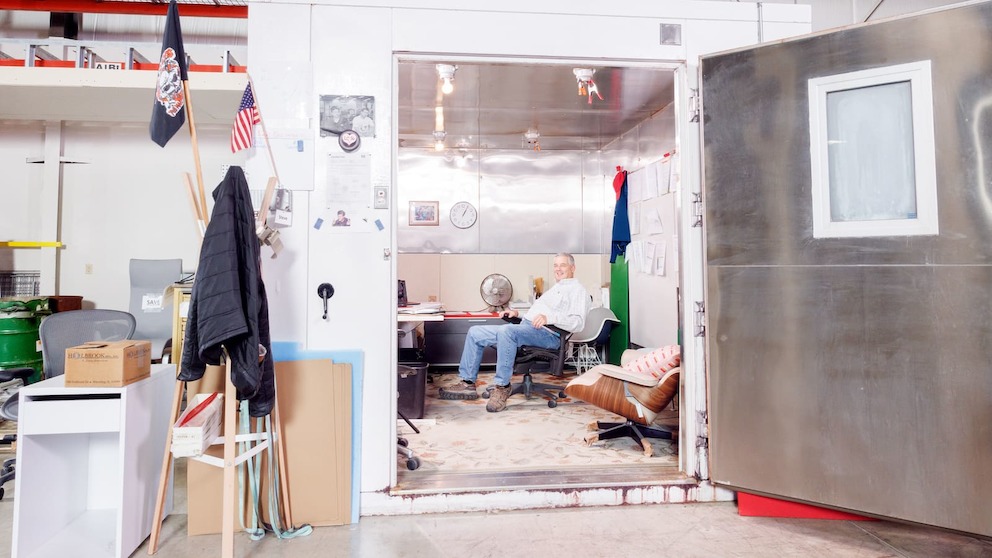