240 Pfund statisches Gewicht stehen für den Haltbarkeitstest der Rückenlehne bereit.
1958 schufen George Nelson und der Eigentümer von Herman Miller, D.J. De Pree, auf Drängen von Charles und Ray Eames einen Ort, in dem Designer mit Produktprototypen und Tests experimentieren konnten. Mehr als sechs Jahrzehnte später ist das Test Lab praktisch nicht mehr wiederzuerkennen. Was einst eine alte Reparaturwerkstatt voller mechanischer Geräte (Kabel, Rollen, Gewichtskanister und sogar pneumatische Komponenten) war, ist heute ein Präzisionslabor in der Größe eines Flugzeughangars, voll ausgestattet mit hochtechnologischen Maschinen, die Geschwindigkeit und Aufprall bis ins kleinste Detail messen können.
Das Labor befindet sich im Herzen der Making-Zone im Design Yard in Holland, Michigan – eingebettet zwischen dem Makers Space und dem Produktdesignstudio. Man könnte es als das Labor eines Tüftlers bezeichnen – oder besser gesagt, als den gigantischen, mit glänzenden, schweren Maschinen ausgestatteten Spielplatz eines Tüftlers. Die Böden sind mit Sicherheitsklebeband markiert, und rote und grüne Lichter flackern aus und an, als würden sie Signale in einer geheimen Maschinensprache senden.
Der Rhythmus der Maschinen, auf denen die Haltbarkeitstest durchgeführt werden, erfüllt die Räume. Gewichtssäcke fallen auf die Sitzfläche eines Stuhls. Armlehnen wippen unter zunehmendem und abnehmendem Druck. Laufrollen drehen sich tagelang – alles im Namen der Wissenschaft, die hinter dem Design steckt.
Die Techniker führen etwa 2.500 verschiedene Tests an Produkten wie Arbeitsstühlen, höhenverstellbaren Schreibtischen und Paneel- und Tischsystemen durch. Bei Belastungs- und Haltbarkeitstest werden Worst-Case-Szenarien nachgestellt: Sitzstangen für Armlehnen, Lehnen für Rückenlehnen, Faltapparate. Die hängenden Regale werden mit immer mehr Gewicht belastet, bis sie zusammenbrechen. Maschinen dehnen die Möbel bis zum Zerreißen. Bei der Verschleißsimulation wird Robotik eingesetzt, um Monate, Jahre oder sogar ein ganzes Leben in einem verkürzten Zeitrahmen nachzustellen. Die Techniker führen häufig ein Reverse-Engineering durch, indem sie einen Fehler reproduzieren. Und scheinbar macht es vielen Spaß zu scheitern. „Alle reden nur von den Stühlen, aber Paneel- und Sitzbanksysteme werden Belastungstests unterzogen, und die sind viel arbeitsintensiver – bis zu 4.000 bis 5.000 Pfund Eigengewicht auf einem System“, sagt Ingenieur Kyle Wright, Prüfungsleiter im Labor.
In einer Ecke des Labors, weit weg vom ständigen Brummen, führen Techniker chemische Tests mit einer Reihe von Bechern durch: Soda, Schweiß, Desinfektionsmittel. Es gibt Kammern, die Hitze, Feuchtigkeit oder Kälte simulieren. Das ist wichtig, wenn Produkte bei jedem Wetter versandt werden. Jedes Problem, das auftritt oder auftreten könnte, wird wissenschaftlich begutachtet und streng analysiert. Im Anschluss an die Prüfung sammelt das Laborteam Rohdaten, um zu entscheiden, ob ein Design die Tests bestanden hat.
Die Richtlinien der BIFMA (Business and Institutional Furniture Manufacturers Association) geben den Industriestandard für die Produktleistung vor. Die Produkte von Herman Miller erfüllen jedoch mehr als nur diese Anforderungen. Beim Haltbarkeitstest der Rückenlehne – oder „Lean-Back“-Test werden mit einer Kraft von 75 bis 100 Pfund 120.000 Zurücklehn-Zyklen durchgeführt. Herman Miller führt 1.000.000 Zyklen durch. Warum? Ganz klar: wegen der Garantie. Viele der getesteten Produkte sind von einer 12-Jahres-Garantie abdeckt: 12 Jahre – aber auch 24 Stunden am Tag, sieben Tage die Woche, 365 Tage im Jahr. Für die Techniker geht es sogar noch um mehr: Ihre Integrität steht auf dem Spiel. „Die Qualität liegt in unserer Verantwortung“, sagt Wright.
Um die Bedeutung von Qualität und Integrität im Test Lab zu verstehen, gehen wir an seinen Ursprung zurück. Zu Nelsons erster Möbelkollektion für Herman Miller im Jahr 1948 gehörte ein Katalog, der in seinem Vorwort mehrere wichtige Grundprinzipien nannte, darunter auch die Qualität (ein guter Vorläufer dessen, was nur ein Jahrzehnt später zum Test Lab werden sollte).
„Was man macht, ist wichtig“, schrieb Nelson. „Herman Miller unterliegt wie alle anderen Unternehmen den Regeln der amerikanischen Wirtschaft, doch habe ich es noch nie erlebt, dass bei der Verarbeitung oder den Oberflächen gespart wurde, um ein gefragtes Preissegment anzupeilen oder aus sonst einem Grund.“
1978 hielt der Designkritiker Ralph Caplan auf dem President's Club Meeting von Herman Miller einen Vortrag zum Thema „Eames und Qualität“. (Der Vortrag wurde später als Essay mit dem Titel „Doing Quality“ gedruckt.) Er schlug vor, ein Design zu entwerfen, das „so gut ist, wie es nur sein könnte“. Diese Idee wurde von einem der Mitarbeiter des Eames Office, Peter Pearce dadurch ergänzt, dass bei jedem kreative Akt auch die „Bereitschaft zum Scheitern“ gegeben sein muss.
Der „Swinging impact“-Wagen ist mit einer beschwerten Abrissbirne ausgestattet.
Durch all diese Tests, bei denen diese Produkte gebogen, gedreht, mit spitzen Gegenständen bearbeitet, fallen gelassen und übergossen werden, können wir die Garantie des Unternehmens erfüllen – und noch einiges mehr. Manche Stühle werden vielleicht jeden Tag von einer anderen Person benutzt, andere wiederum von Generation zu Generation weitergegeben. „Wir möchten etwas entwickeln, das Bestand hat“, sagt Curt Vanduren, leitender Techniker im Test Lab. „Manche fragen: ‚Warum kostet der Stuhl so viel?‘ Dann erkläre ich, was alles in so einem Stuhl steckt. Und was von diesem Stuhl während seiner gesamten Lebensdauer erwartet wird.“
Wright sagt, dass es drei bis fünf Jahre dauern kann, bis ein Produkt auf den Markt kommt – mit sechs bis zehn verschiedenen Versionen, die jeweils getestet werden müssen. Einige der Tests sind einfach – andere definitiv nicht. Er erinnert sich an einen besonders denkwürdigen Systemtest vor vielen Jahren, bei dem es um Büropaneele und Trennwände ging. „Wir haben alles an ein Hydrauliksystem angeschlossen, um zu simulieren, wie Regale und eine Arbeitsplatte heruntergezogen werden“, sagt Techniker Steve Arendsen. „Als es versagte, explodierte es förmlich. Die Paneele sind geflogen.“
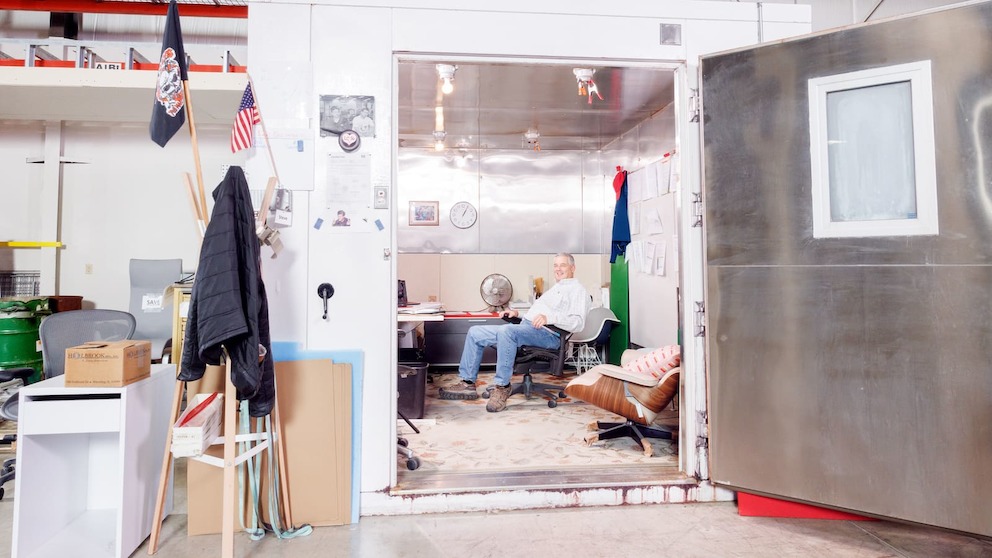
Der Techniker Steve Arendsen findet einen Moment der Ruhe im Test Lab in seinem Büro – einer umgebauten Feuchte-Schockkammer.
Da diese Tests oft die Zerstörung von Produkten beinhalten können, werden in frühen Entwicklungsstadien oft rudimentäre Materialien verwendet. „Die Stühle durchlaufen den gesamten Prozess und bestehen zunächst nur aus Karton und Klebeband“, sagt Vanduren. Und es sind nicht nur die ersten Designs, die auf den Prüfstand gestellt werden – jede Phase der Produktlebensdauer wird getestet. Für Techniker, die sich für diese Stücke begeistern, ist das oft eine Qual. Arendsen sagt: „Es ist eine Schande, wenn ein schöner Aeron in Flammen aufgeht.“
„Die Qualität liegt in unserer Verantwortung“.
– Kyle Wright, Testleiter